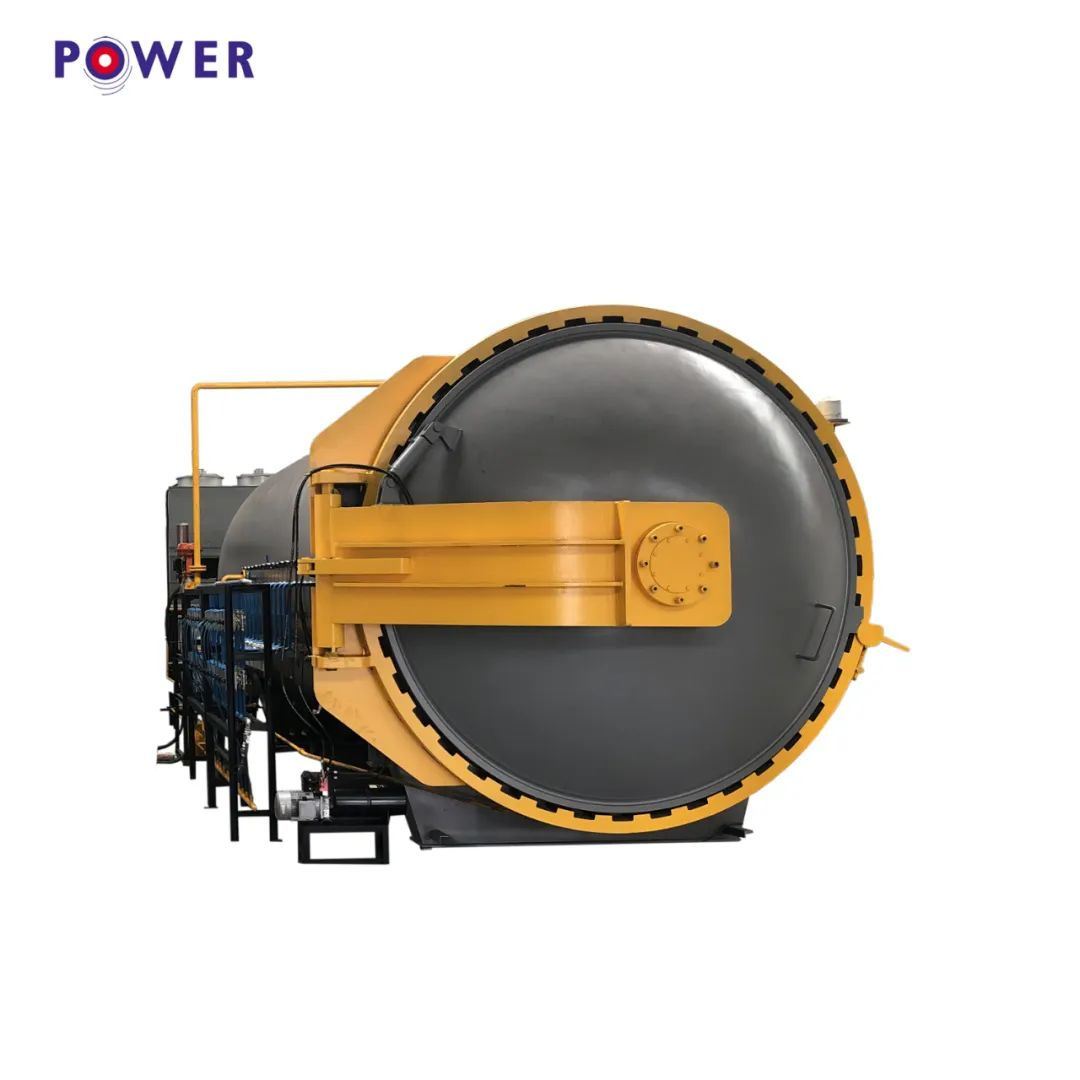
The impact of vulcanization on the structure and properties of rubber:
Vulcanization is an important step in the manufacturing process of rubber products, which is the process of transforming from linear structure to body structure, bringing comprehensive changes including physical and mechanical properties, temperature resistance, solvent resistance, and corrosion resistance, enhancing the value and application range of the product.
The structure and properties of rubber undergo significant changes before and after vulcanization. The rubber molecules before vulcanization have a linear structure with van der Waals forces acting between them, exhibiting good plasticity and elongation, as well as solubility. During the vulcanization process, molecules are triggered and undergo chemical cross-linking reactions, forming a network structure where molecules are bonded by chemical bonds.
The structure and properties of vulcanized rubber mainly include:
Structure: chemical bonds, position of cross-linking bonds, degree of cross-linking, and cross-linking
Performance: Mechanical properties (constant elongation strength, hardness, tensile strength, elongation, elasticity), physical properties, chemical stability after vulcanization
The vulcanization process can significantly alter the properties of rubber. Taking natural rubber as an example, as the degree of vulcanization increases:
Changes in mechanical properties: increased elasticity, tensile strength, tensile strength, tear strength, and hardness, decreased elongation, compression permanent deformation, and fatigue heat generation
Changes in physical properties: The air permeability and water permeability decrease, cannot be dissolved, can only swell, heat resistance improves, chemical stability improves, crosslinking reaction eliminates highly active groups or atoms, making aging reaction difficult to carry out. The network structure hinders the diffusion of low molecules, making it difficult for rubber free radicals to diffuse.
The vulcanization conditions, including pressure, temperature, and time, are the key factors that determine the vulcanization results. The vulcanization pressure has an important impact on preventing the formation of bubbles in the rubber material, improving the compactness of the rubber material, and filling the mold with the rubber material. It can also improve the adhesion between various layers (rubber layer and cloth layer or metal layer, cloth layer and cloth layer) in the product, and improve the physical properties of the vulcanized rubber (such as bending resistance).
The vulcanization temperature is the basic condition of the vulcanization reaction, which can directly affect the vulcanization speed, product quality, and economic benefits of the enterprise. Raising the vulcanization temperature can accelerate the vulcanization speed and improve production efficiency, but excessive vulcanization temperature can lead to problems such as rubber molecular chain breakage, vulcanization reversal, decreased mechanical properties of rubber materials, and decreased strength of textiles. It can also shorten the scorching time of rubber materials, causing local rubber deficiency and uneven vulcanization of products. Therefore, the selection of vulcanization temperature should comprehensively consider factors such as rubber type, vulcanization system, and product structure.
Determining vulcanization conditions - including pressure, temperature, and time - is a complex process that requires consideration of multiple factors.
Vulcanization pressure: The choice of vulcanization pressure mainly depends on the design and requirements of rubber products. In general, the selection of pressure is mainly determined by the shape, size, and complexity of rubber products. The greater the pressure, the better the fluidity of the rubber, which can better fill the mold. At the same time, high pressure can effectively prevent the generation of bubbles and improve the compactness of the product. However, excessive pressure may lead to excessive flow of the rubber material, causing distortion in the shape of the product.
Sulfurization temperature: The vulcanization temperature directly affects the speed and quality of the vulcanization reaction. The higher the temperature, the faster the vulcanization reaction, but it may cause the breakage of rubber molecular chains, affecting the physical properties of the product. An appropriate vulcanization temperature can ensure a good vulcanization speed without causing significant thermal damage to the rubber material.
Sulfurization time: The vulcanization time is directly related to the vulcanization temperature. Higher temperatures may require shorter vulcanization times, and vice versa. In general, the selection of vulcanization time needs to consider the type of rubber material, vulcanization temperature, and the thickness of the product. The optimal vulcanization time determined through experiments can ensure that rubber materials achieve optimal mechanical properties and aging resistance.
Overall, determining the vulcanization conditions is a process that requires comprehensive consideration of various factors such as the type of rubber material, product shape, vulcanization equipment, etc. In actual production, it is usually necessary to conduct multiple experiments and gradually optimize the vulcanization conditions to obtain the best product performance.
Post time: Jan-09-2024